Modernizing Warehouse Operations for Manufacturing OEMs – Taking Steps with AI & Digital Twin
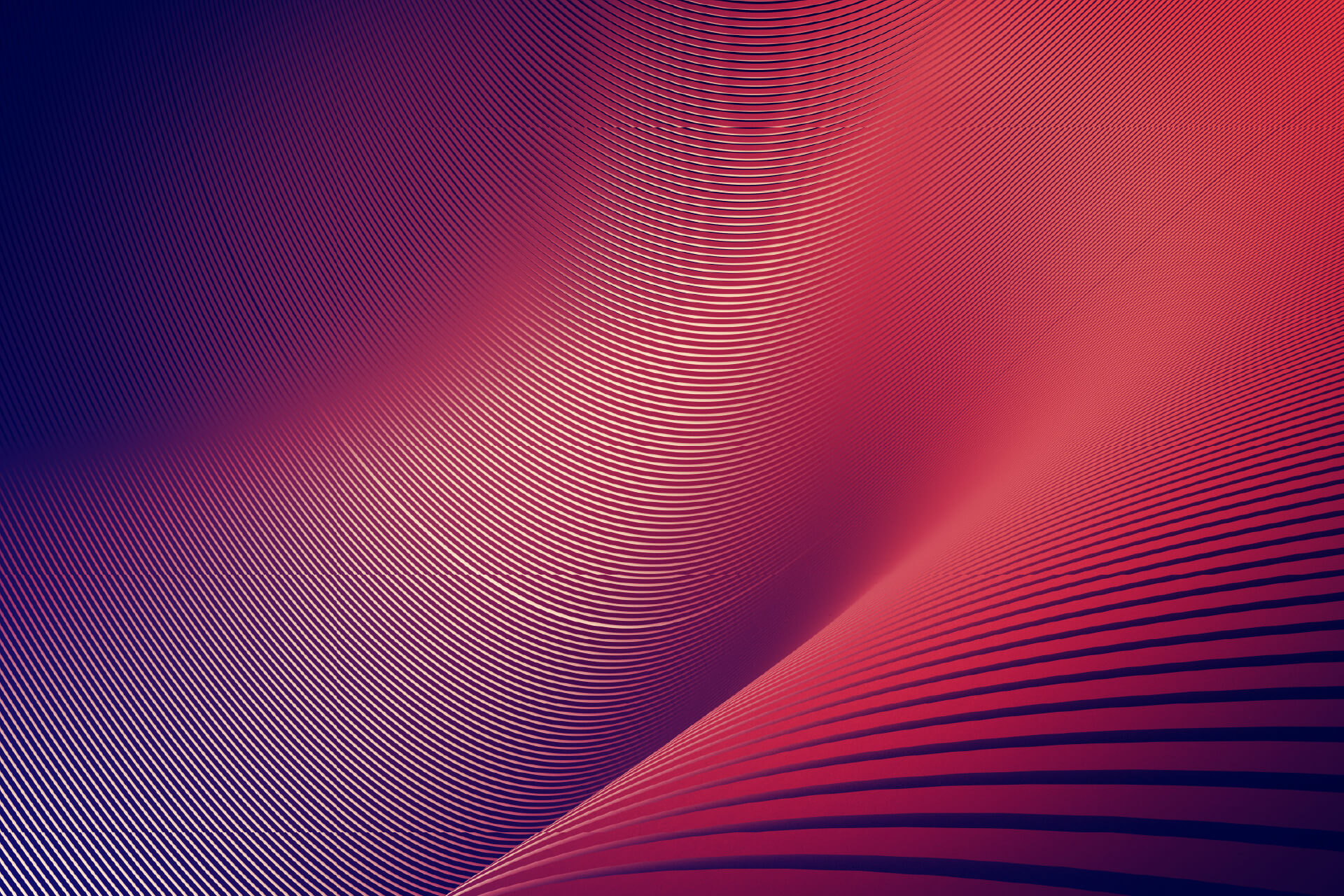
Warehouse operations at Manufacturing OEMs have often been a secondary priority for supply chain and operations teams seeking transformation. Warehousing is inherently complex, and this complexity multiplies with an increasing number of SKUs, material types, suppliers, categories, and interdependencies. These operations indirectly impact production and customer service.
Incorporating AI and Digital Twin technologies enhances the strategic decision-making capabilities of operations managers. By providing comprehensive insights and predictive analytics, these solutions empower management to make data-driven decisions that align with long-term business objectives and market demands. Improvements in real-time visibility and optimization can drive significant gains in overall warehouse operational efficiency (15-20%) and achieve cost reductions (5-10%).
Industrial automation in warehouse operations—such as Automated Storage and Retrieval Systems (ASRS), pickers, sorters, material movers (AGVs/AMRs), and cobots/robotic arms—significantly improves operational efficiency and productivity. Warehouse automation can drive productivity and efficiency gains of up to 25-30%.
Key transformation opportunities with a direct impact on operational efficiencies include addressing challenges in:
- Visibility: Even with advanced WMS, WES, and EWM implementations, the ability to virtually replicate and visually reference the warehouse, inventory, inventory flow, and operational KPIs is often limited. Operators and supervisors often rely on Excel sheets, tables, and basic graphs (enabled by tools like Power BI or Tableau). This can result in erroneous reporting and increased manual effort. A lack of real-time visibility leads to delayed or reactive decision-making and increased operational inefficiencies.
- Decision-Making: Limited visibility hampers and delays decision-making. Often, operators and supervisors spend most of their time firefighting and fixing operational glitches. Furthermore, while data is available via WMS and ERP systems, a lack of advanced analytics and real-time insights means decision-making can be biased and dependent on the subjective judgment of personnel on the floor. Moreover, by the time action is taken, the damage may already be done.
- Operational Efficiency: Manufacturing warehouse operations are often labour-intensive, manual, and time-consuming. This applies to picking/kitting, stocking, put-aways, inventory stock-keeping, and material movement. While some WMS systems can provide optimization in picking and routing, the correct allocation of inventory, based on various types, categories, movement, and frequency, is often a manual process that is not frequently updated. This results in lost time, increased costs, and reduced operational efficiency.
AI & Digital Twins as a Two-Pronged Solution
AI and Digital Twin capabilities enable solutions (tools/applications) that capture real-time data and visually represent it in 2D/3D layouts. This provides a single, real-time or near-real-time snapshot of operations.
First, gain a clear view of existing operations and flows to understand key gaps and their impact on the business and operations. Digital Twin-based tools/applications can rapidly build a visual representation of current (As-Is) operations and flows, often within minutes. These tools ingest data from existing WMS/ERP systems (or even Excel spreadsheets) and provide a 2D/3D representation of end-to-end warehouse operations.
Second, adjust controllable parameters and optimize based on material flow, order load, material types/categories, and other relevant factors. Simulate multiple scenarios and analyze cost factors alongside performance measures. Given the inherent complexities, improvement factors can be weighed and prioritized to select the most optimal scenarios.
Finally, leverage the simulation tool/application to provide AI-driven recommendations for restock allocations and material movements. With Digital Twin capability, these tools can provide a visual representation of the To-Be scenarios and operations. The integration of AI and Digital Twin capabilities fosters a culture of continuous improvement within the organization.
As these technologies evolve, they offer new opportunities for refining processes, reducing waste, and enhancing overall productivity. This adaptability ensures that warehouse operations remain competitive and resilient in the face of changing market conditions and customer expectations.
This approach can improve operational efficiency with relatively low investment, as these modern tools are comparatively inexpensive and leverage existing data sources (such as WMS, ERP, or spreadsheets). Upon execution of these recommendations, the achieved benefits can be measured in near real-time.
In summary, AI and Digital Twin capabilities enhance warehouse operations through real-time visibility, optimization, and simulation/scenario planning. This results in significant improvements in operational efficiency and reductions in operational costs. Ultimately, adopting AI and Digital Twin capabilities represents a significant step forward in the evolution of warehouse operations. By embracing these cutting-edge technologies, organizations can achieve greater visibility, efficiency, and agility, positioning themselves for sustained success in an increasingly complex and dynamic business environment.
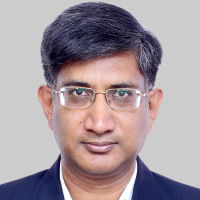
Abhishek has over 23 years of consulting experience with global manufacturing clients in Digital Supply Chain and Industry 4.0. An expert in manufacturing operations, industrial and supply chain processes, and digital transformation, he is an engineering graduate and holds a postgraduate degree in Operations and Supply Chain.